ABSTRACT – LEAN principles
One of the main tools for increasing the effectiveness of project management, is the The LEAN methodology. It is a systematic approach to identifying and eliminating waste through continuous improvement. The purpose of LEAN is to produce more with fewer resources by eliminating waste. The LEAN methodology is derived from the organization strategy and its goal is to supply value added to the customer, and profit to the organization.
The definition of value added is:
- Something for which the customer is willing to pay
- It changes the product or the information
- It is done right at the first time
The main technique of the LEAN philosophy is to establish a continuous flow from suppliers through the internal organizations to the final customer. This paper will show that by implementing LPD practices during the development process, leads to:
- Supplying a product that meets the needs of the customer.
- Shortening the development and production cycle times.
- Reducing the development and production costs.
Applying LEAN principles in product development and project management
Implementing LEAN in production is relatively easy because the product is tangible and the flow is visible. You can detect waste from: over production, inventories of work in process, defects, movement of products and people, and so on. In the development environment, it is similar, but instead of dealing with products and manufacturing flow, we deal with engineering data creation and flow. The problem is that it is difficult to see the data, because it is buried in the documents, computers, but most of it is invisible because it exists inside people minds.
In a project that requires interfacing with other external systems and a number of sub-systems which may be designed by different functional departments; the most important project information is hidden in the interfaces among all those domains, (figure 1). This information will be revealed only if all the parties of those domains integrate in a structured way and analyze the project, (LPD Workshop). If not, this information will surface later during design / production in an uncontrolled manner, as a risks, generating errors and defects, which will cause schedule delays, rework, or even the re-development of projects.
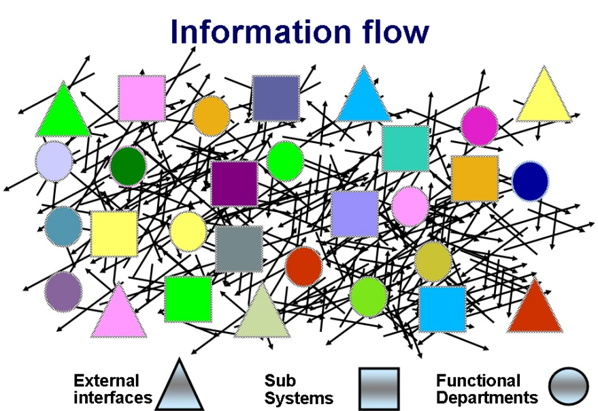
LPD Workshop
The workshop is a concentrated effort of selected team members focused to achieve a step function of data creation and flow, which will be utilized during all project processes. The most effective phase for this workshop, is initiation of new project. In this stage, there is not enough information on the project, but the most important decisions have to be made. The purpose of the workshop is to increase the fidelity and understanding of the information so that the right decision can be made in a timely manner.
The workshop has three components: (Figure 2)
- Multidisciplinary Integrated Product Team (IPT)
- LPD tools relevant to the workshop
- Workshop facilitator
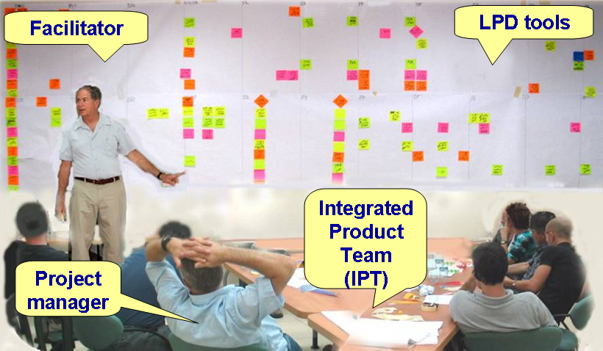
The first part of the workshop is documenting the reality of the current situation of the project, using a combination of LPD tools. The role of the facilitator is to ask the right questions in order to present the real project status in a visual and understandable way.
The next step is to identify the obstacles, problems and also the opportunities for improvement. This is done by applying a brainstorming technique. The final stage of the workshop is preparing a “to do list” of corrective actions, improvements, responsibilities and a time table.
The results and outcome of this workshop are:
- Templates for capturing new data and information
- A focus on value creating activities
- New insights of the development process
- Real time reallocation and synchronization of activities
- Team identity and emotional commitment
- Common language among team members
- To do list identifying new corrective actions
About a month after the workshop, there must be a follow up meeting to verify that the corrective actions have been taken and the workshop target has been achieved. The workshop success is dependent on the implementation of those corrective actions. It is the project manager role to monitor and document progress.
Integrated Product Team ( IPT) Workshop
The first step of implementing LPD is building the Integrated Product Team (IPT). It defined as:
- A multidisciplinary team
- Accountable for the product / assignment
- Team co-located (optional)
- There is a documented agreement that summarizes team accountability and responsibility
This is the most important workshop, and some times the most difficult. Participants are coming from different functional departments and organizations, and are not use to teaming and working together. It is hard to move from your comfort zone and work with new team members. The team members have to learn how to work under two bosses; the functional department manager, and the project manager or the IPT team leader. Each team member has to understand their role on the team, and what output and input he has to supply to the team. This working together mechanism, IPT, enables the free flow of information inside the project among the team members, and among all the subcontractors of the project.
Project managing and planning Workshops
In this workshop, all the main team members that participate in the project must participate. The team members build together the project plan in a visual way on time table.
In most of the time, this workshop identify lack of: requirements, resources, configuration, work contents, communication and responsibilities. It is also discover risks and on the other hand opportunities for project improvements. All this information is documented on a visual project plan, and a “to do list” format that include corrective action for implementation, team member responsibility and time table
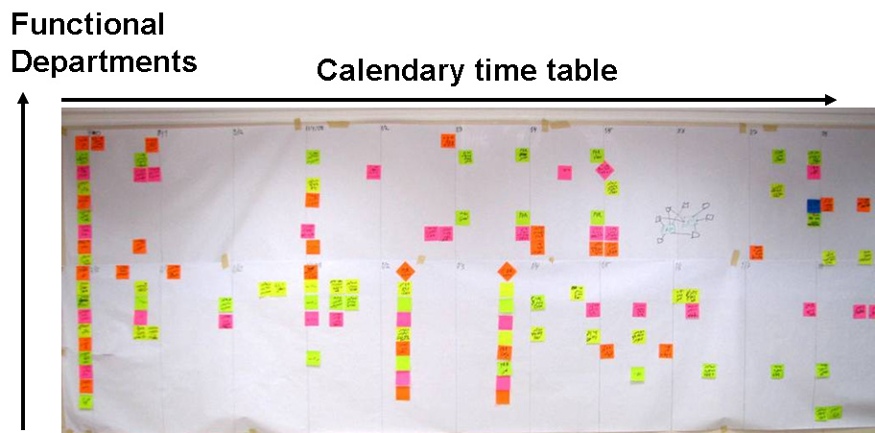
The outcome of the workshop is a development plan with a realistic time table which is agreed upon and committed to by the entire team.
In addition, by participating and working together in building the development plan, the participants transition from individuals to a cohesive and productive team. The team members assume responsibility and accountability; which is the main driver for project success.
Quality Function Deployment (QFD) Workshop
One of the main reasons of project delays are: waiting for information and requirements, or unclear requirements. The causes of this delay is lack of a structure process of requirements development, from the customer down to the detailed design.
The QFD methodology enables the team members to understand the customer needs and translate those needs into detailed requirements and detailed design in an efficient and fast way. QFD also enables us to develop the requirements and allocate them to the design teams at the very beginning of the project. It reduces almost completely the waste of redesign, and dramatically shortens the time from project kick off to the design process and project building. The QFD workshop can reduces the time frame of understanding requirements from a few months to a few days.
Cost reduction Workshop
Usually during project design, product cost is in low priority, because the main attention is to implement customer requirements. This leads to a high final project cost, which lowers organization profit, and sometimes creates losses. In order to maintain the initial target cost, (or lower), we have to apply the Design to Cost, (DTC), methodology. If the cost exceeds the target cost, we have to apply a cost reduction workshop, using the DFMA (Design for Manufacturing & Assembly), methodology. This methodology enables the team members to challenges the design in a structural way with a brainstorming technique. The outcome of the workshop are creative ideas for cost reduction that leads to a significant product cost reduction. Typically, teams achieve about 60% cost reduction before the PDR, and 30% during the detailed design phase.
Applying a workshop to a specific project
The workshop can be applied at any point of the develop and design process. However, the most effective phase is in the early stage of design. Each workshop must be well prepared to achieve the maximum value and efficiency. The preparation for the workshop includes
- Understanding project situation / problems.
- Determining the workshop targets and verifying that the targets can be achieved within the time frame of the workshop.
- Selecting the tools that will be applied during the workshop.
- Determining material that has to be prepared for the workshop.
- Leveling expectations between the project manager and the facilitator.
- Selecting workshop team members and workshop time table.
Conclusion
In today’s environment, each of the development team members is tied to his computer. Therefore, organizations need a mechanism for gathering all cross-functional team members together in a methodological way to enable them to work as a team.
After facilitating more than 2000 workshops, I am convinced of the efficacy of this methodology. The project team will achieve their target goals in a fast and effective manner rather than the traditional method.